
The normal operation of modern industrial equipment is inseparable from the support of efficient heat dissipation systems. Among them, the radiator assembly, as one of the key components, plays a vital role in maintaining the long-term stability and prolonging the service life of the equipment.
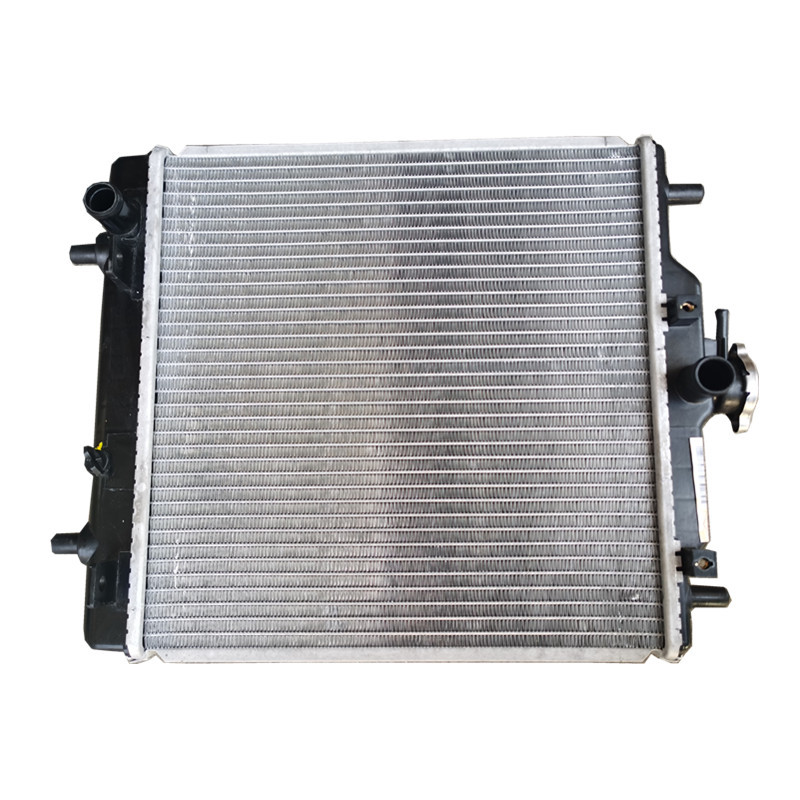
Cooling core: The main task of the radiator assembly is to take away heat from the high temperature area and dissipate it to the surrounding environment. This process relies on the combination of a precisely designed network of pipes and an efficient heat transfer medium. For example, in automobile engines or large mechanical equipment, water-cooled radiators use circulating liquid to absorb the excess energy generated and then release it, thereby achieving a cooling effect.
Of course, it is not enough to know the working mechanism. You also need to pay attention to the specific elements that make up these systems to make a wise choice.

Quality Choice: Material selection directly affects the performance of the product and its cost considerations. Aluminum fins are the first choice for their good thermal conductivity and lighter weight, while copper tubes are suitable for high humidity operating environments in special areas such as chemical plant pumping stations due to their higher corrosion resistance. In addition, the use of advanced manufacturing processes such as welding and sealing technology further improves overall reliability.
Although the market offers many different styles and specifications of products for consumers to choose from, it is not easy to find the one that best suits their needs.

Adapt worry-free: It is important to ensure that the size of the purchased radiator matches the installation space. Also consider whether the rated power range covers the expected load requirements. For some industry-specific applications (such as data center server clusters), there may also be issues such as noise level control standards that need to be carefully weighed and compared before making a decision.
The purchase of new equipment is important, but if the lack of proper maintenance methods, it is likely to shorten its actual service life!

Maintenance tips: Regular cleaning of surface attachments helps to maintain good ventilation conditions and reduce the probability of clogging. In addition, timely check the looseness of fasteners to prevent leakage caused by cracks in connection parts due to vibration. Following the simple steps above can give you a greater return on your investment.
no matter how much theoretical knowledge there is, it needs practical verification ~ let's take a look at some successful implementation cases to share.

case sharing: a well-known beverage manufacturer introduced a new efficient energy-saving heat dissipation device to replace the old version in its filling assembly line renovation project, and found that the output per unit time increased significantly and the frequency of failure maintenance decreased significantly, saving considerable operating expenses; another power facility operation and maintenance service provider has deployed an intelligent monitoring platform to track and record the health status of the main transformer accessories at each site in real time. Early warning of potential risks and hidden dangers has greatly improved the score of customer service satisfaction evaluation index.
Scientific and technological progress is endless. I believe that more innovative achievements will emerge in the near future to change the face of our lives.

future trend: at present, researchers are actively exploring whether nanoscale coating treatment technology can further enhance the intermolecular force strength between traditional metal substrates to achieve lower contact thermal resistance effect. At the same time, graphene, a new two-dimensional carbon material, is also regarded as a potential development direction worthy of attention and expectation due to its unique physical and chemical properties.
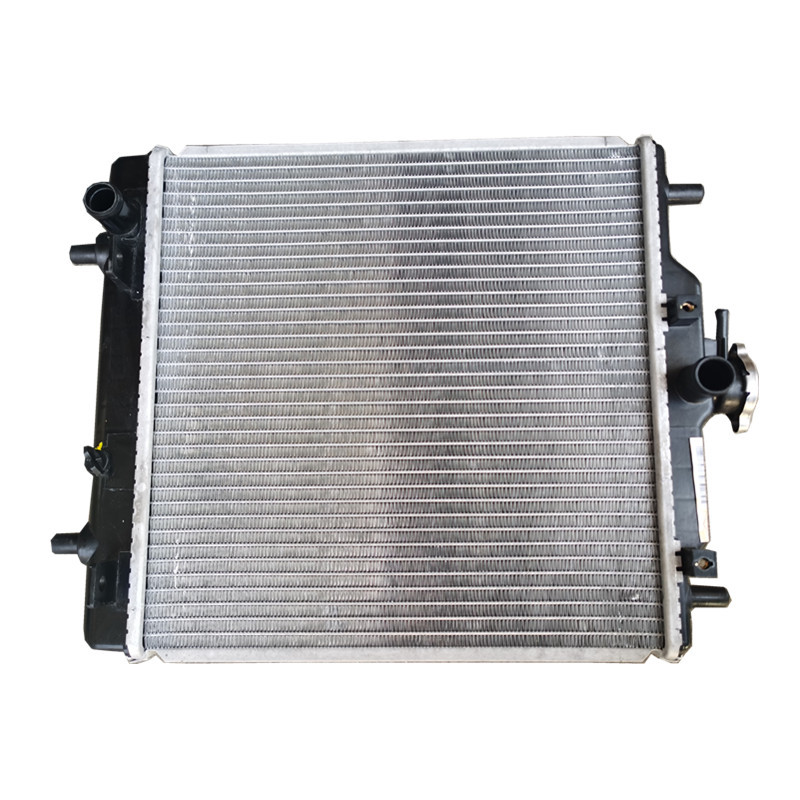